Comparing two heat exchangers
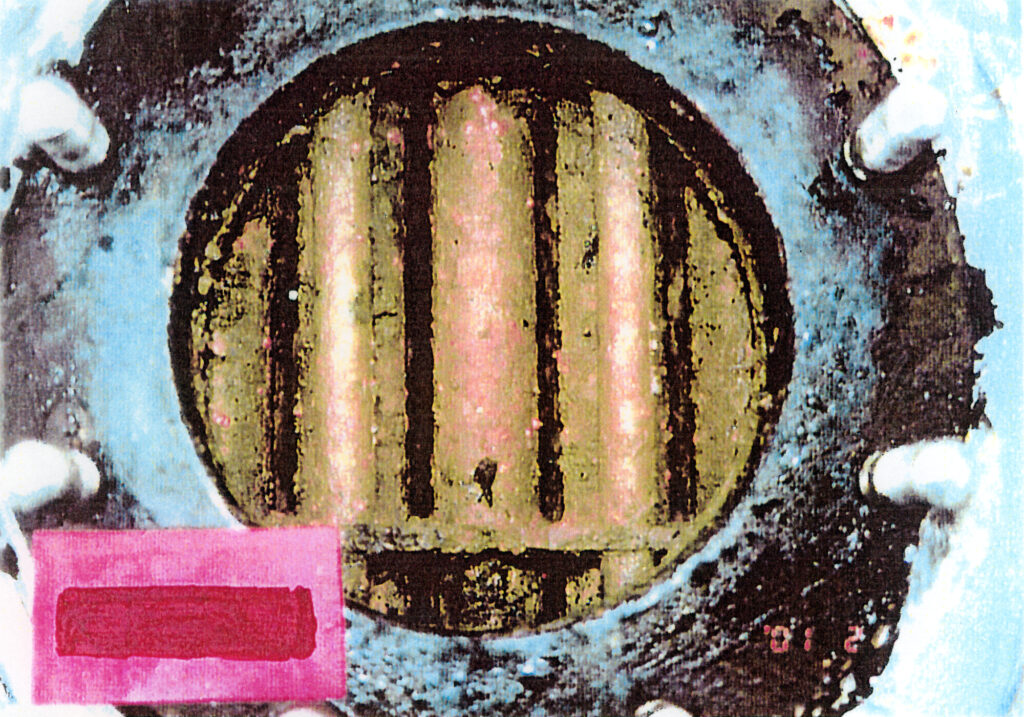
Heat exchanger #1 without Non-Scalor
Mass amount of calcium scale deposit rebuilt up after the factory’s regular cleaning in Aug. 2000. *The photo taken in Feb. 2001
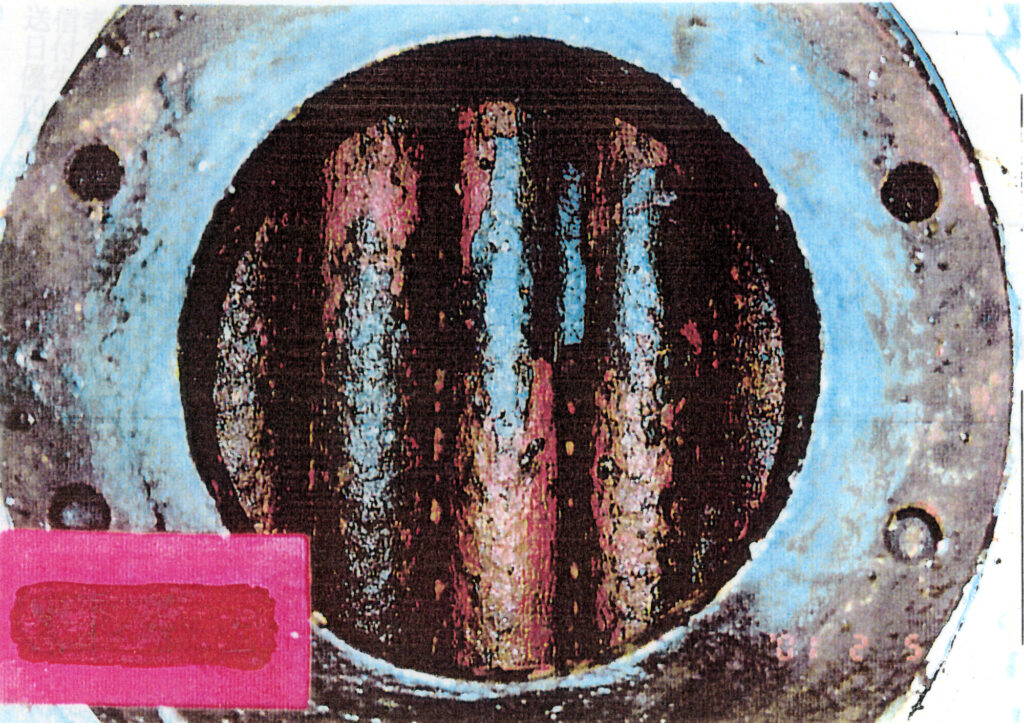
Heat exchanger #2 with Non-Scalor
Calcium scale being controlled after the factory’s regular cleaning and Non-Scalor installation in Aug. 2000. *The photo taken in Feb. 2001
Summary
In general, the growth of calcium scale inside heat exchangers affects their heat exchanger efficiency and even disrupts factory operation in the worst-case scenario.
To protect multi-pipe heat exchangers from calcium scale issues, Major Chemical Co. Ohita factory ran a test trial of Non-Scalor.
First, the factory implemented regular cleaning on two heat exchangers and installed Non-Scalor on one of them on Aug. 2000, and then confirmed the device’s performance six months later.
In Feb. 2001, no calcium scale adhesion was seen on the one equipped with Non-Scalor, while the other without Non-Scalor had a mass amount of calcium scale being built up again.
There will no longer be a decrease in the heat exchange efficiency or disruption on the factory’s product lines.
Profile
Facility | Major chemical Co. Kyushu factorty in Japan |
---|---|
Type of pipeline | Factory’s circulating cooling water pipework system |
NMR installation date | Sep.14, 2000 |
Installed unit | One Non-Scalor NS-75 on a heat exchanger inlet pipe |